1、原材料准备
材料选择:
交叉导轨加工通常选用优质的钢材,如轴承钢(GCr15)或高碳铬钢。这些钢材具有高硬度、高强度、良好的耐磨性和疲劳强度等特点,能够满足交叉导轨在高负载、高精度运动下的性能要求。例如,GCr15 钢材含碳量约为 1%,铬含量约为 1.5%,这种成分比例使得钢材经过适当的热处理后,能够获得良好的硬度和耐磨性。
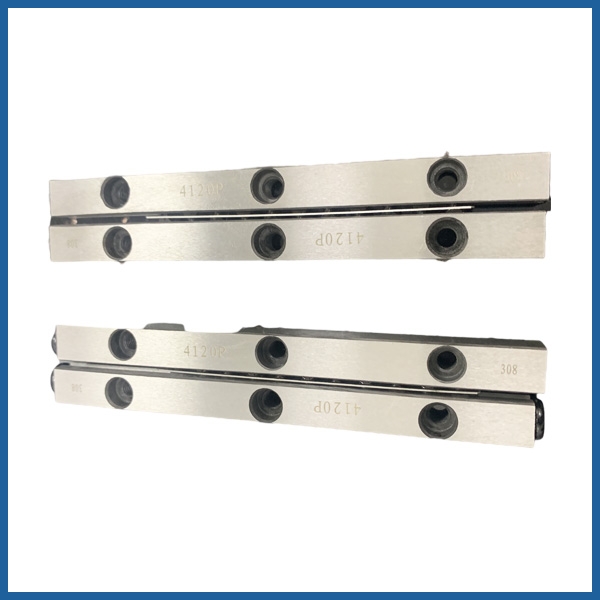
材料检验:在材料投入加工前,需要进行严格的检验。包括检查材料的化学成分是否符合标准,通过光谱分析仪进行检测,确保钢材中的各种元素含量在规定范围内。同时,对材料的硬度、金相组织等进行检验,例如,使用硬度计检测材料的初始硬度,通过金相显微镜观察钢材的金相组织,判断是否存在缺陷,如夹杂物、偏析等,这些缺陷可能会影响导轨的质量和性能。
毛坯制备:根据交叉导轨的设计尺寸,将选定的钢材切割成合适的毛坯尺寸。切割方法可以采用锯切或火焰切割等。对于精度要求较高的情况,一般采用锯切,以减少切割过程中的热影响区和变形。毛坯的尺寸要预留一定的加工余量,余量大小根据导轨的尺寸、形状复杂程度和加工精度要求而定,一般单边余量在 3 - 5mm 左右。
2、粗加工阶段
铣削加工:首先使用铣床对毛坯进行粗铣。主要目的是去除大部分余量,初步形成导轨的大致形状。例如,对于交叉导轨的基础平面和侧面,采用端铣刀进行铣削,设定合适的切削参数,如切削速度、进给量和切削深度。切削速度一般根据刀具材料和工件材料来确定,对于硬质合金刀具铣削 GCr15 钢材,切削速度可以在 100 - 200m/min 之间;进给量一般在 0.1 - 0.3mm/z(每齿进给量);切削深度可以根据余量大小设置为 3 - 5mm。通过粗铣,使导轨的平面度和尺寸精度初步达到一定要求,为后续加工打下基础。
钻孔和镗孔(如果有):如果交叉导轨上有安装孔或油孔等结构,在粗加工阶段需要进行钻孔和镗孔操作。钻孔时,要根据孔的尺寸和精度要求选择合适的钻头,例如,对于精度要求较高的安装孔,先使用麻花钻进行钻孔,然后再用铰刀进行铰孔,以提高孔的精度。镗孔则用于加工精度要求更高的孔,如一些与其他部件配合的定位孔,通过镗床或加工中心的镗孔功能,精确控制孔的尺寸、圆柱度和位置精度。
3、半精加工阶段
精铣加工:在粗加工的基础上,进行精铣操作。使用精度更高的铣床和刀具,进一步提高导轨的平面度、直线度和尺寸精度。精铣时,切削速度可以适当提高,进给量和切削深度减小,以获得更好的表面质量。例如,切削速度可调整到 150 - 250m/min,进给量为 0.05 - 0.15mm/z,切削深度为 0.5 - 1.5mm。精铣后,导轨表面的粗糙度一般可以达到 Ra1.6 - Ra3.2μm 左右。
磨外圆和平面(如果有):对于交叉导轨的外圆部分(如果需要高精度的外圆表面)和一些关键平面,采用外圆磨床和平面磨床进行磨削加工。磨削是一种高精度的加工方法,可以有效提高表面的形状精度和粗糙度。在磨削过程中,控制砂轮的转速、进给速度和磨削深度等参数。例如,外圆磨削时,砂轮转速一般在 1500 - 3000r/min,工件进给速度在 0.5 - 2m/min,磨削深度在 0.01 - 0.05mm。通过磨削,使导轨的外圆精度达到 μm 级,平面的平面度可以达到 0.005 - 0.01mm。
4、精加工阶段
精磨加工:这是提高交叉导轨精度的关键步骤。使用高精度的磨床,如数控平面磨床和成型磨床,对导轨的工作表面进行精磨。精磨时,砂轮的粒度更细,一般选用 80 - 120 目甚至更细的砂轮,以获得更好的表面质量。磨削参数更加精细,例如,磨削速度可以在 20 - 30m/min,进给量在 0.005 - 0.01mm/dst(每双行程进给量),磨削深度在 0.002 - 0.005mm。精磨后的导轨表面粗糙度可以达到 Ra0.4 - Ra0.8μm,平面度和直线度可以达到更高的精度,满足高精度设备对交叉导轨的要求。
研磨和抛光(可选):对于一些对表面质量和精度要求极高的交叉导轨,如在半导体设备或高精度测量仪器中使用的导轨,需要进行研磨和抛光处理。研磨可以使用研磨膏和研磨工具,通过手工或机械方式,进一步降低表面粗糙度,消除精磨后的微小痕迹。抛光则是在研磨的基础上,使用抛光轮和抛光剂,使导轨表面达到镜面效果,表面粗糙度可以降低到 Ra0.1 - Ra0.2μm 以下,同时提高导轨表面的光泽度和耐磨性。
5、热处理工艺
淬火处理:为了提高交叉导轨的硬度和耐磨性,一般需要进行淬火处理。将导轨加热到合适的淬火温度,对于 GCr15 钢材,淬火温度通常在 820 - 860℃之间。加热速度要适当控制,避免导轨因热应力过大而产生变形。淬火介质可以根据具体要求选择,如水淬火或油淬火。水淬火冷却速度快,能获得较高的硬度,但容易产生淬火变形和裂纹;油淬火冷却速度相对较慢,淬火变形较小,但硬度可能稍低。淬火后,导轨的硬度可以达到 HRC60 - HRC65 左右。
回火处理:淬火后的导轨存在较大的内应力,需要进行回火处理来消除内应力,稳定组织,提高韧性。回火温度一般在 150 - 250℃之间,回火时间根据导轨的尺寸和批量而定,一般为 2 - 4 小时。通过回火,导轨的硬度会略有下降,但韧性和尺寸稳定性得到提高,能够有效防止导轨在使用过程中出现断裂或变形的情况。
6、表面处理与装配准备
表面防锈处理:为了防止交叉导轨在储存和运输过程中生锈,需要进行表面防锈处理。常见的方法有涂防锈油、磷化处理或电镀等。涂防锈油是一种简单有效的方法,将防锈油均匀地涂覆在导轨表面,形成一层保护膜,防止氧气和水分的侵蚀。磷化处理则是通过化学反应在导轨表面形成一层磷化膜,这种膜不仅具有防锈作用,还可以提高导轨与润滑剂之间的附着力。电镀(如镀硬铬)可以进一步提高导轨的耐磨性和耐腐蚀性,同时使表面更加光亮。
精度检验与配对装配(如果有):在完成加工和表面处理后,需要对交叉导轨进行全面的精度检验。使用量具和仪器,如三坐标测量仪、激光干涉仪等,对导轨的尺寸精度、形状精度、位置精度等进行检测,确保各项精度指标符合设计要求。如果是成对使用的交叉导轨(如 V 型和平面型组合),还需要进行配对装配,通过精确的调整和配合,使两根导轨之间的平行度、等高性等达到最佳状态,以保证运动部件在导轨上的平稳、高精度运动。